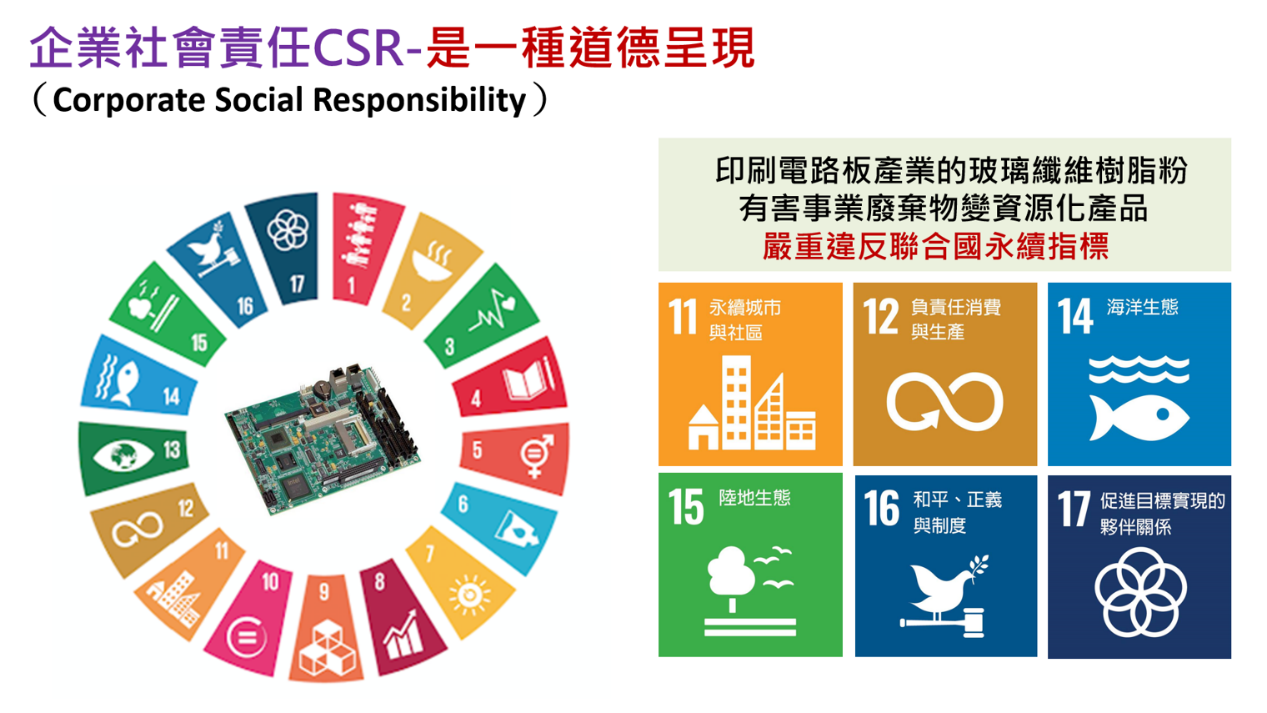
企業社會責任(Corporate Social Responsibility;CSR)是許多大公司常常掛在口頭上的詞彙,係指企業營運應負其於環境(Environment)、社會(Social)及治理(Governance)之責任,亦即企業除了追求股東(stockholders)最大利益外,還必須同時兼顧到其他利害關係人(stakeholders)的權益,包括員工、消費者、供應商、社區與環境等。
台灣電子產業發達,尤其具備先進半導體、PCB高階技術製造優勢,如5G基礎建設中所需的晶片、ABF載板、IC載板、多層高頻硬板等高階產品已開始發酵;台灣廠商近年在台紛紛擴大投資計劃,布局5G通訊高階與智慧製造新產能;台積電更被戲稱為護國神山。這些極具競爭力、甚至在全球舉足輕重的產業,如能在追求經濟利益之餘,也盡到企業社會責任,才是國家之福;否則錢他們賺走,卻留下許多環境與社會承受不了的負荷,令人情何以堪?
台灣PCB產業全球市佔第一的社會責任,在哪?
以印刷電路板(PCB)為例,2019年台灣印刷電路板產業,全球市佔率高達31.4%,產值是世界冠軍。這個無論是家電、電腦、通訊產品、手機、穿戴式裝置、車用電子都需要的電路基板,隨著各類電子產品的推陳出新而蓬勃發展,印刷電路板製造技術也與時俱進,從單/雙面板、多層板、軟板,精進到軟硬結合板、IC載板、高密度多層板及MSAP類載板高階製程。
然而業者可能只把眼光放在印刷電路板的產品技術發展與市場擴展,卻鮮少把心思放在製造過程以及產品銷售使用後所產生的廢棄物上,而讓我國農地、魚塭,受到難以磨滅的傷害!全球市佔第一的社會責任,在哪?
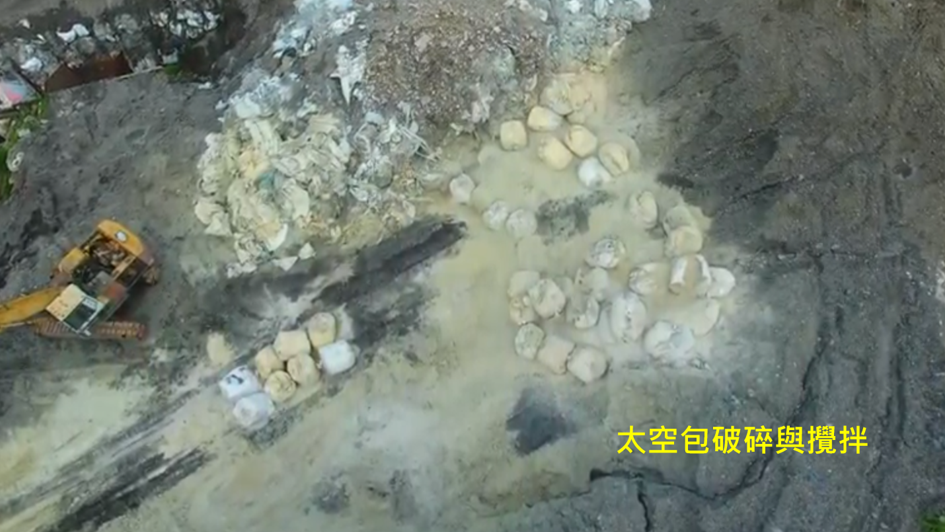
鍇霖土資場將有害事業廢棄物混合其他事業廢棄物
2018年,環保團體在屏東鍇霖土資場上發現一包一包太空包堆積如山,裡面有來源不明的粉狀物,或呈白色、黃色、淡黃色,重金屬含量超高,於是向屏東環保局檢舉,環保局當時回應是玻璃砂,環團無法置信!兩年後環團才從屏東地檢署不起訴書中赫然發現,果然不是玻璃砂,而是銅與樹酯含量超高的玻璃纖維樹酯粉,且其銅溶出量已經超出有害事業廢棄物認定標準。這些玻璃纖維樹酯粉來自哪裡?原來是桃園三家收受廢印刷電路板的處理業者,包括毅川、中德、樺欣。
據了解,鍇霖於2016-2019年共收受2286.5噸來自桃園這三家處理機構的有害玻璃纖維樹脂粉,土資場內不但埋了大量的太空包,更把其當作填地材料,與煤灰、鑄砂等事業廢棄物混合後回填至農地與魚塭。
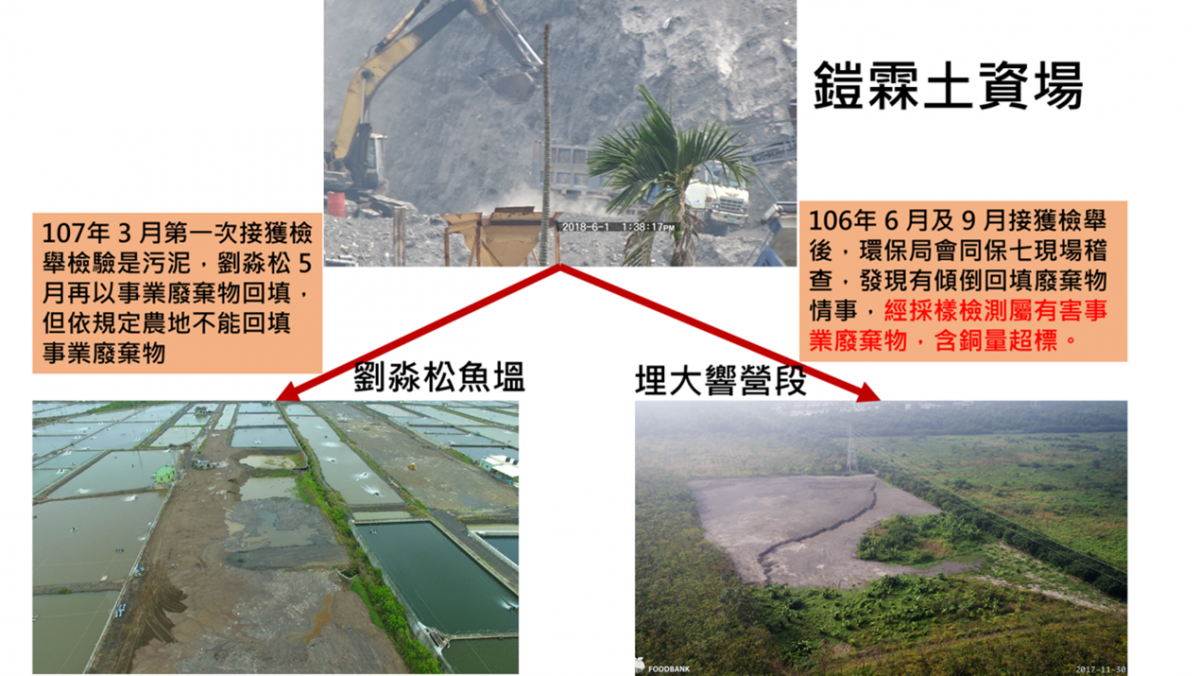
2020年11月14日(星期六),時代力量陳椒華委員與台南社大環境小組成員隨同環保署南區督察大隊再度到現場勘查,那一包包裝著有害玻纖樹酯粉的太空包還是堆在那裡,於是採了兩個樣,送環保署認可的實驗室檢測。送驗的兩個樣品銅溶出量分別是136 mg/L及166mg/L,皆超出有害事業廢棄物認定標準中的TCLP溶出標準(銅為15mg/L),分別超標9倍及11倍之多。
另以王水消化法檢驗這兩個樣本的銅含量,則分別為37,900mg/kg及26,500 mg/kg(即3.79%與2.65%),符合桃園市政府核發、鄭文燦市長蓋章背書的三家廢棄物處理機構許可證中的資源化產品「玻璃纖維樹脂粉」的品質標準(銅含量<5%)。
不起訴書透漏的荒謬――包庇一條龍
從不起訴書中我們才知道,檢警環於2017年起就開始調查本案,且總共採樣了3次;若加上台南社大採樣一次兩件,時代力量採樣一次兩件,這5次7件樣品銅毒性溶出量全部超標,可說這些玻纖樹脂粉100%檢測都屬有害事業廢棄物。
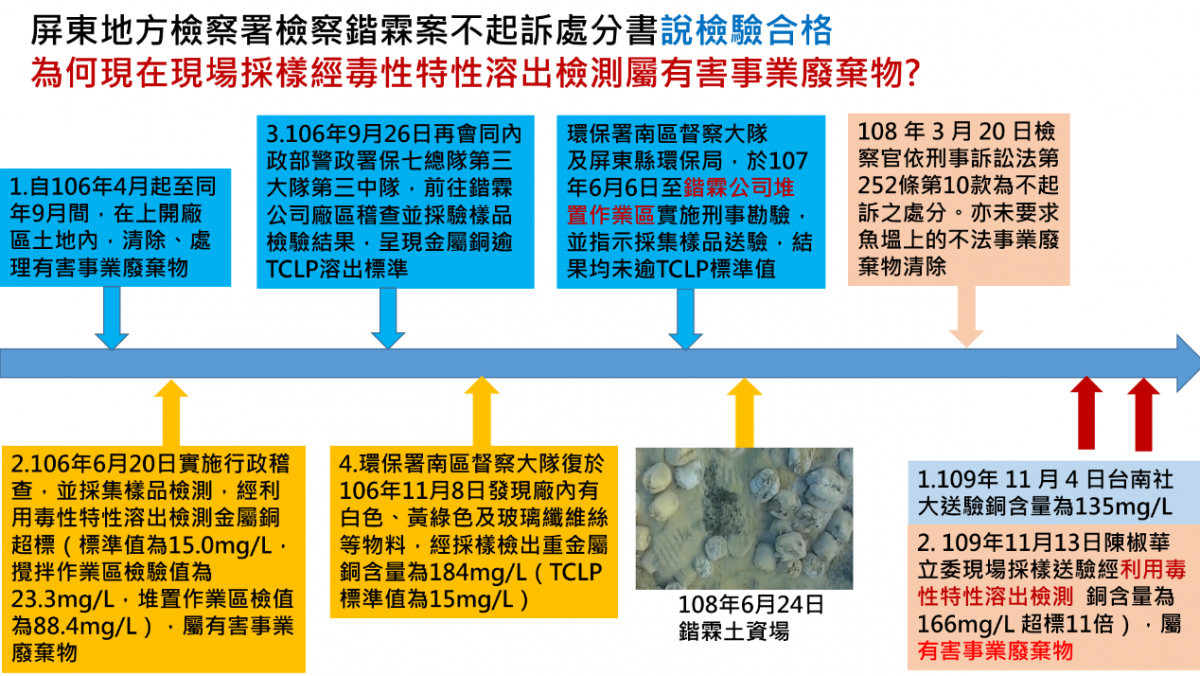
既早已知情,屏東環保局為何指鹿為馬,把玻璃纖維樹脂粉稱作是玻璃砂?環保署為何一直不提出毒性溶出實驗的數據?本案因長期以來環保官員提供不實資訊,讓檢調可將污染行為人順利放水,更嚴重破壞體制下有害事業廢棄物認定原則與產品再利用的基本標準,至今屏東檢調不起訴、屏東環保局對填滿事業廢棄物的魚塭不依廢清法要求清除,並放任土資場變成有害事業廢棄物掩埋場,這樣包庇一條龍的行為,實是動搖國本。
而桃園PCB產業佔全台產值一半,桃市政府本應帶頭落實印刷電路板廢棄物合理妥善處理,怎會將有害事業廢棄物印刷電路板及其粉碎料經處理後仍然有害的玻璃纖維樹脂認定為資源化產品?而早已介入調查的環保署,在發現桃園環保局不合理的許可核發後,為何不下令取消玻璃纖樹酯粉資源化產品的資格?
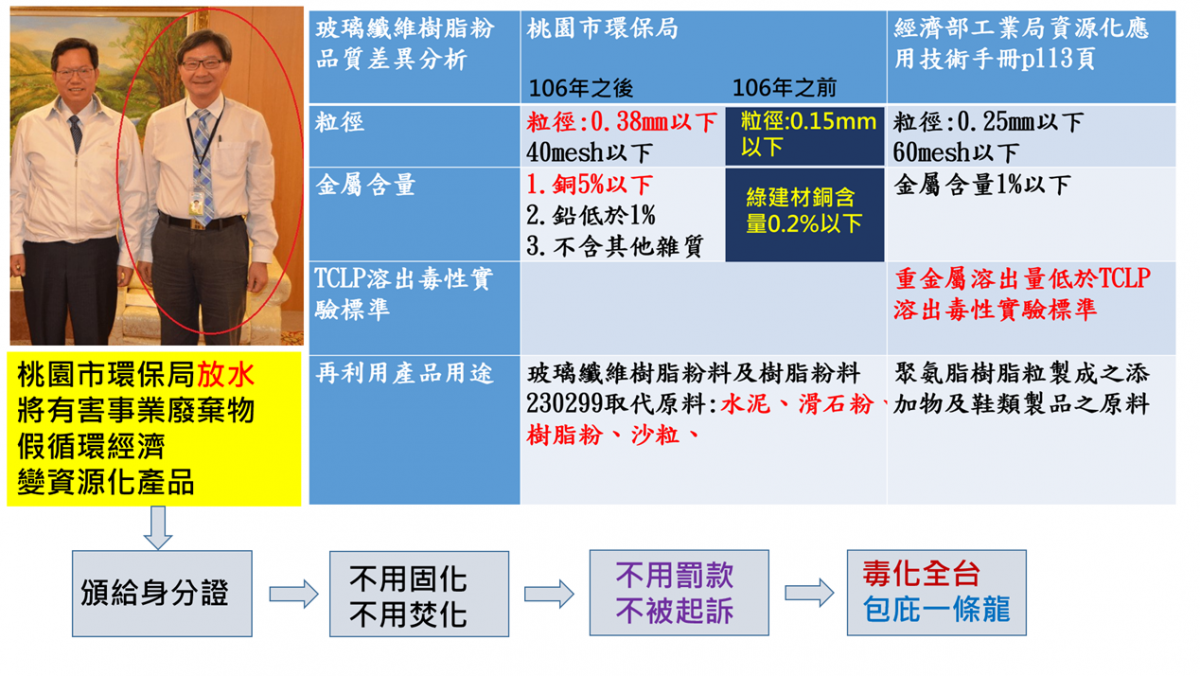
為何桃園環保局可透過審查會將有害事業廢棄物放水為資源化產品?
為何中央與地方要一味包庇這些不肖的業者?難道是要讓印刷電路板生產者享有便宜的廢棄物清除處理成本,提高其經濟競爭力?這不但將產業內部成本外部化,更毒化全台。這樣嚴重的行為明顯違反聯合國6個永續指標:永續城市與社區、負責任的消費與生產、海洋生態、陸地生態、和平正義與制度、促進目標實踐的伙伴關係。
開發友善環境同時能真正資源化的處理技術 方是負責任的展現
PCB的主要原材料為銅、玻纖布及樹脂,經由基板廠製造成銅箔基板(Copper Clad Laminate;CCL),隨後銅箔基板送至電路板廠經過數十道製程,不同製程則會加入使用如金、鈀、化學品、水等物質,最終形成了印刷電路板,製程繁複。
但對比之下,毅川、中德、樺欣三家的處理技術相對單純,他們以粉碎剝離技術,來處理屬有害的印刷電路板及其粉碎料:拔除電子元件的廢印刷電路板須先經初步粉碎,再經磁選與渦電流分離步驟回收含鐵與非鐵金屬物質,然後經一系列篩分與分選過程,可分別取得混合金屬(貴金屬、錫/鉛、銅、鋁)、玻纖樹酯粉與粉塵。但問題在於處理後的玻纖樹脂粉還是屬於有害事業廢棄物,裡頭還有含量不小的金屬物質未取出,顯然處理技術有問題。1
這讓我們看到,這個產業可以為了生產賣錢的產品,不惜投入繁複製程,但為了節省處理有害廢棄物的成本,委託以廉價技術產出假資源化產品並危害大地的業者,這不是缺乏社會責任的展現嗎?如果我們的PCB產業是透過這樣的成本外部化方式,拿到全球市佔率(31.4%)第一,這不是很可恥嗎?
檢視目前廢印刷電路版的處理技術,主要有三,除了前面講到的機械破碎分選方式之外,還有火法冶金及濕式冶金方式。其實機械破碎分選方式不是完全不可取,而是必須把印刷電路板粉脆磨細到極細顆粒,才能將金屬物質和玻纖樹酯粉有效分離,但如此處理成本就必須提高,也比較耗能。經濟部工業局編印的《印刷電路板業資源化應用技術手冊》中即曾舉一再利用個案,其玻纖樹酯粉的品質標準為粒徑60mesh以下,金屬總含量1%以下,與前述桃園這三家處理業者許可中的資源化產品品質標準(粒徑40mesh以下、銅含量5%)相比,就可看到玻纖樹酯粉粒徑越細、金屬含量就越低的關係;也可看到後者許可太過寬鬆,是桃園市政府透過公權力協助業者將處理成本外部化,從而降低了技術水平,增加了其資源化產品的環境風險。
至於火法冶金方式,是將拔除電子元件的印刷電路板廢料經機械粗破碎後,送入焚燒爐中焚燒,將所含約40%的樹脂分解破壞,所產生廢氣則以冷卻水將其急速降溫至180°C以下,再經活性碳噴注及袋濾式集塵器等空氣污染防治設備處理後排放;剩餘殘渣即為裸露之金屬及玻璃纖維,經粉碎後即可送往金屬冶煉廠進行金屬回收。日本DOWA 公司即採取此法處理廢印刷電路板,回收包括金、銀、鉑、銠、鈀、釕、銅、鉛、鋅、鎘、錫、鎳、石膏、鉍、硒、碲、銦、鎵、鍺、銻等多達19種的金屬及非金屬。2此法優點是金屬回收率較高,又可回收部份熱能,缺點是焚化過程會產生有害物質如戴奧辛與多溴二苯醚(因為印刷電路板會添加溴化阻燃劑)以及有害的飛灰。
至於濕法冶金,則是先將廢印刷電路板粉碎後,以酸、鹼溶解金屬,再透過電解、離子交換樹酯、活性碳吸附等裝置,回收各種貴重金屬。日本田中貴金屬(TAKANA)即是採取此種方式。2此法優點是可以選擇性地溶取鎳、銅等金屬,也可以回收高純度的金,缺點是會產生廢酸、廢鹼等廢棄物。
前面三種方法各有優劣,是否有其他方法,不產生空污、不衍生廢棄物,且能有效把廢印刷電路板中的金屬物質分離出來的?有的,目前已有學者研究以水熱液化法處理廢印刷電路板:其先把廢印刷電路板破碎成2mm的顆粒,再以400°C的超臨界水處理,在鹼的催化下,可以把玻璃纖維樹酯粉中的Epoxy樹酯變成含62%以上苯酚的油狀液體,溴化阻燃劑經處理後的溴化物,會跑到水相中,只有0.03ppm存在油相中,如此油相就可以安全地再利用。這方法可去除94%的Epoxy。處理後的固相為富集的各種金屬與玻璃纖維,應該也很容易再分開來。如此其再利用就比較不會有問題,同時可提昇貴重金屬的回收率。3
好消息是,台灣在應用亞臨界或超臨界流體於生產製程上已累積許多實務經驗,因此也有技術能力將其應用在廢棄物處理上。而成立超臨界流體協會推廣此技術的高雄金屬工業研究發展中心,也有套實驗室規模的水熱設備,用來開發污泥液化及碳化的技術。
PCB產業若要展現企業社會責任,應該檢視國內外既有處理業者的技術,委託對環境影響最小、技術最先進的處理業者;同時共同投入資金,與高雄金屬工業研究發展中心或其他鑽研水熱處理技術的研發者合作,發展及建立對環境最友善、最能資源化的水熱處理設施;並共同委託第三方機構,監督其廢棄物的處理及循環利用過程,莫再讓遺害流竄到農田魚塭、危害我們的環境與食安。
附註:
1.〈廢印刷電路板資源化技術-粉碎剝離技術,〉,經濟部工業局「工業廢棄物清理與資源化資訊網」。
2.〈廢棄物再利用技術〉,郭貹隆,財團法人綠色生產力基金會。
3.“Chemical recycling of printed circuit board waste by depolymerization in sub- and supercritical solvent”, Eyup Yildirir, etc., University of LEEDs, UK, 2015.
- 作者:黃煥彰/中華醫事科技大學護理系副教授,台南社區大學環境行動小組召集人,看守台灣協會理事。
- 發表日期:2021年2月2日。